影响变压器损耗因素有哪些?如何降低?
电力变压器是电力系统中最重要的设备之一,是保证供电可靠性的基础。随着整个国民经济的快速发展,对变压器的需求将继续增加。然而,随着电力变压器装机量的增加,其自身消耗的能量也越来越大,这与中国倡导建设节能社会不一致。因此,影响变压器损耗主要有3个因素:空载损耗,负载损耗,杂散损耗,那么这几个因素该如何降低?
引文作者:上海盖能电气市场部(专注干式变压器30年)电话:189 1886 3098(微信同号)
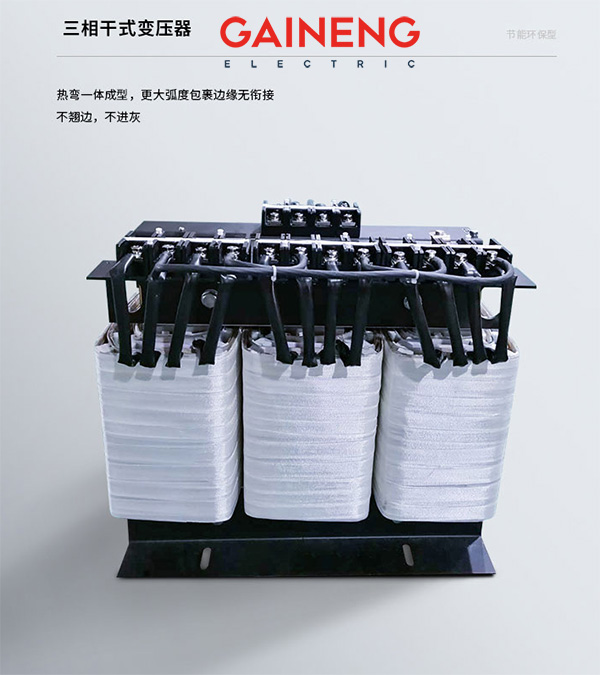
一、降低空载损耗的方法
空载损耗是变压器的重要参数,占变压器总损耗的20%~30%。为了减少空载损耗,必须减少铁芯总量、单位损耗和工艺系数。减少空载损耗的主要方法如下:
(1)采用高导磁硅钢片和非晶合金片。普通硅钢片厚度0.3~0.35mm,损耗低,可使用0.15~0.27mm。同时,如果采用阶梯堆积,铁损可减少8%左右。激光照射、机械压痕和等离子处理可以减少高导磁硅钢片的损耗。非晶合金片和含硅量为6.5%的硅钢片,其涡流损耗小于普通高导磁硅钢片。
(2)降低工艺系数。工艺损耗系数与硅钢片材料、冲剪设备是否退火、夹紧程度等诸多因素有关。合理调整冲剪设备的刀具精度也很重要。
(3)改进铁芯结构。铁芯不冲孔,不绑扎玻璃胶带,端面涂固化漆,相间用高强度钢带绑扎。连接心柱两侧上下夹件的拉板采用非磁性钢板。大容量铁芯片不涂漆,以提高填充系数和冷却性能。铁芯两轭采用强压工装和粘合剂,成为一个坚固、平整、垂直、精度高的整体。减少铁芯的搭接宽度可以减少损失。每减少1%的搭接面积,空载损失将减少0.3%。铁芯中不同品牌的硅钢片会消耗能量,因此应少混或不混。
(4)减少铁心窗的尺寸。将绕组不变匝绝缘(厚度)改为变匝绝缘。例如,根据冲击电压分布12万/110变压器,高压绕组一端和调压段的匝绝缘厚度为1.35mm,其他段为0.95mm。因此,在减小窗口尺寸后,降铁重量为1.67%。在安全的前提下,合理缩小高、低主空道之间的距离,减少饼间油道,缩小相间距离,加强绝缘处理(加角环、隔板等)。绕组采用半油道结构,缩短了心柱的中心距离、铁重和铁损。
(5)设计无共振铁芯。铁芯的共振频率设计在合适的频率段,使其无法产生强共振,对降噪效果明显,可以节约为降噪而使用的能源。
(6)采用卷铁芯变压器和立体铁芯变压器。卷铁芯比传统的叠片铁芯少4个尖角。连续卷绕充分利用了硅钢片的定位,采用了退火工艺,减少了附加损失。对于R型卷铁芯,截面占空系数接近100%。三维铁芯的轭呈三角形,比平面卷铁芯的轭重减轻25%。这些因素表明,卷铁芯和三维铁芯更节能。
二、降低负载损耗的方法
负载损耗占总损耗的70%~80%,包括绕组直流电阻损耗(基本损耗)、导线涡流损耗、绕线间环流损耗、导线损耗和结构件(如夹板、钢压板、箱壁、螺栓、铁芯拉板等)。).减少负载损失的主要方法如下:
(1)限制漏磁造成的附加损失。计算安匝平衡,根据结果调整安匝;绕组采用低-高-低或高-低-高排列;限制扁线的宽度和厚度;根据磁场选择最合适的换位方法;使用换位导线或组合导线。
(2)缩小主绝缘和纵绝缘结构的尺寸。高压绕组采用等冲击电压梯度分布技术,可缩小纵绝缘尺寸;绕组之间采用薄纸筒和小油间隙;瓦楞纸是主绝缘;形状与等电位完全相同的成型件,角环形状符合等位线形状,以分瓣成型角环为结构件;绕组内径绕在绝缘纸上,但线段中间设有轴向油道;多采用缩醛漆包线,用QQ-2或QQB缩醛线代替0.45毫米厚的纸包扁线。由于前两种匝绝缘为2×(0.056~0.079)毫米,绕组填充系数高,满足匝绝缘要求;多采用圆柱形绕组。由于没有饼间油道,冷却主要依靠轴向垂直油道,散热好,填充系数和冲击特性好,匝均匀,短路力小;适当缩小主绝缘(径、端)之间的距离。
(3)根据计算采用相关工艺。根据冲击计算,确定垂直绝缘结构、垫块、支撑、金属倒角保持良好形状;计算漏磁场和涡流分布,指导换位方式;绕组轴向均匀分布,心柱绑带采用非磁性材料;心柱和轭铁部分设置特殊屏蔽,缓解电场;压力调节绕组逐层分开;工艺采用组装,内绕组直接绕在绝缘筒上,高度严格控制,直径公差小,套装间隙小,采用热套新工艺,采用整体托盘和压板,绕组换位采用迪尼松纸,带压干燥,绕组放置在绝缘干燥室,防止受潮。
(4)采用低损低阻导线。采用上引法拉拔无氧铜线,如铜连续挤压机。如果可以用在变压器上,可以节能降体积,有一定的应用前景。
(5)利用绝缘结构的特点设计可缩小体积。利用变压器油液体电介质的特性,适当设置覆盖层、屏障、屏蔽和绝缘层;利用油的距离效应将隔板添加到小油间隙中;利用油的体积效应采用瓦楞纸;利用油中绝缘层的厚度效应增加绝缘,提高击穿电压,但不宜过厚;利用油中隔板的最大场强距离特性设置隔板。
(6)采用先进的绝缘结构。采用适用绕组,提高填充系数,采用轴向油道新型螺旋(或连续)绕组,有效降低绕组体积。非金属或非磁性材料的压缩结构用于漏磁集中部分,漏磁通槽用电磁屏蔽路化,负载损失可降低3%~8%。
(7)首选绕组内部保护。绕组内部保护措施包括电容环、静电线匝、串联补偿(附加蛋糕间电容)、等电位屏幕、纠结绕组或内屏蔽绕组。它们都具有减少冲击下作用于主和纵绝缘的过电压,从而减少变压器的体积和能耗。
(8)采用长圆等绕组与Yyn0连接,降低高度节能。采用长圆形铁芯,绕组或椭圆形绕组或矩形带圆角绕组在实践中比传统圆形截面节能。Yyn0比Dyn11连接的接头电压低,三项可共用一盘接头开关,结构简单,体积小。前者比后者对500kVA变压器重2%,铁重6%,油重11%,节材节能。对于干式变压器,绕组越高,上下温差越明显,有利于散热节能。
三、减少杂散损失的方法
杂散损耗是负载损耗中的一个特例,因此单独讨论了减少它的方法。杂散损耗包括结构件(铁芯夹件、屏蔽环等)的损耗。通过导体(套管座)的损耗;平行导体(通过大电流导线)的损耗和油箱的损耗。减少杂散损耗的方法主要有以下几种:
(1)根据磁分析和物理测量,采用小型铁芯夹件,取消单相中心柱铁芯垫板,增加铁芯表面的间隙,对铁芯拉板和漏磁场中的结构件(如螺栓)采用低磁性或非磁性材料,可减少内部结构的杂散损失。
(2)对于套管出线盒和箱盖的一部分,仔细配置导线以控制磁场,采用铜板屏蔽或非磁性材料,套管盖采用铝制成。硅钢板压板也可以设置在绕组和夹件之间,以吸收夹件和油箱之间的磁通量。将带状有色金属埋在磁场最强的地方,可以减少大电流套管和导线部分的杂散损失。(3)对于大变压器,沿箱壁内置磁导率高的硅钢板进行磁分路,吸收箱壁磁通称为磁屏蔽;或使用导率高的有色金属铜和铝作为衬里,产生涡流的反作用,减少进入油箱壁的漏磁和称电屏蔽。一般来说,磁屏蔽优于电屏蔽,可以减少油箱的杂散损失。
(4)定量计算油流回路,采用挡板,合理分隔绕组,实现均匀冷却,优化波纹油箱、片式散热器、冷却器、节能风扇、油泵,获得最经济的节能冷却方少杂散损失。
(5)采用玻璃纤维增强塑料风扇,效率高,噪音低。用新冷却器代替旧冷却器,采用变频调压电源冷却器,可减少辅助设备的损失。